Inventory management: why should you implement it in your business?
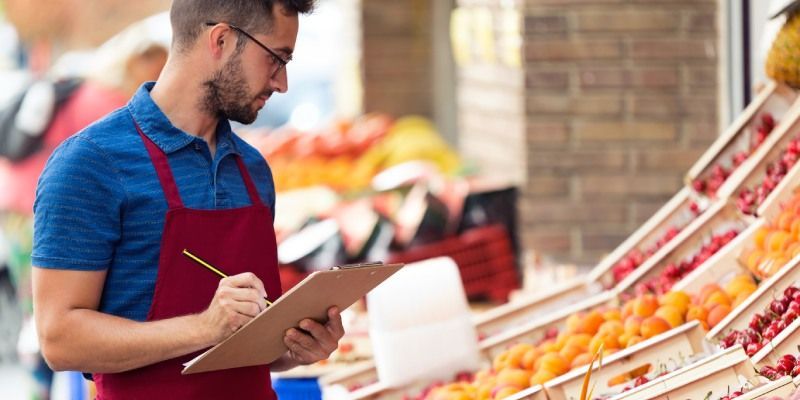
How can a business avoid the challenges associated with inventory shortages or the excess of inventory and its impact on financial health? In all companies, every resource is critical to the manufacture of their distinctive products. That is where inventory management plays a critical role. Learn what it looks like.
Inventory management: why is it important?
In the food and beverage industry, this management is a crucial factor for business success. Basically, it is about maintaining an optimal balance between:
- Having enough products in stock to meet customer demand.
- Avoiding the accumulation of excess that can generate waste or additional storage costs.
Business impact
Proper inventory management has a direct impact on the profitability and competitiveness of companies. Thus, when properly carried out, it allows the following aspects:
1. Control costs associated with the acquisition, storage, and handling of products (Flores et al., 2023). Therefore, maintaining adequate inventory levels avoids:
- Overstocking, which can result in losses due to obsolescence.
- Product shortages, which affect sales and customer satisfaction
2. Properly deal with food and beverage shortages, which can lead to dissatisfied customers and lost sales. Also, it helps with overstocking, that negatively impacts food freshness and rotation.
3. Influence food safety and the quality of supplies.
4. Minimize food losses.
5. Adjust to trends and changes in demand. This, in turn, improves the competitive position in the market.
Inventory management strategies
Strategies in this process are fundamental in any company, especially in the food and beverage sector. Some good practices in this area are the following.
Forecasting systems based on historical data and trends
Using forecasting systems based on historical data and market trends will help forecast future demand more accurately. For example, it can be said that, during summer, a company anticipates an increase in demand for ice cream and cold beverages. After that, it adjusts its inventories and marketing strategies to meet customer needs.
Implement inventory rotation policies
Doing so will minimize obsolescence and maximize product freshness. For example, a supermarket places high importance on the proper rotation of fresh supplies, such as seasonal fruits and vegetables.
Employing computerized inventory management systems with technologies
Its purpose is to improve real-time tracking and visibility of inventory. Let us take the case of a dairy company that implements a machine learning model to optimize efficiency and reduce waste in cheese manufacturing. A 1% improvement in yield represents a $250.000 cost savings (FasterCapital, n.d.).
Establish strong relationships with suppliers and distributors
These logistics players are allies in facilitating timely inventory replenishment. As a result, companies are reevaluating their supplier management strategies to foster innovation.
For example, a company can establish strategic agreements with key suppliers to ensure a steady supply of raw materials. Additionally, these agreements include just-in-time deliveries. All of this minimizes warehousing costs and reduces lead times.
Enjoy the benefits of inventory management
The benefits of maintaining proper inventory control are significant: in addition to reducing costs, it optimizes storage space. It also increases operational efficiency.
Thus, having proper control of your products is the path to efficiency and business success. It is time to take action and turn this information into concrete results for your business.
Bibliographic references
- FasterCapital. (n.d.). Adoptar la tecnología para reducir costes de forma sostenible.
- Flores, X., Cota , Y., & Loredo, R. (2023). Redistribución de inventario con base en clasificación ABC para mejorar el flujo de materiales en una empresa productora de alimentos en Sinaloa, México. Ingeniería Industrial, 65-80.
- Hoyos, Y. (2023). Gestión de inventarios de producto terminado en el área de logística de la empresa Industria de Alimentos ZENÚ. Tecnológico de Antioquia Institución Universitaria.
- Miranda, A. (2023, October 26). Optimiza la gestión de inventario en tu comedor industrial con estos 7 consejos. LinkedIn.